【TOC導入事例 B社】残業を減らしながら生産量UP ! 残業3 分の1に、 生産量は1.7 倍に!
課題と効果
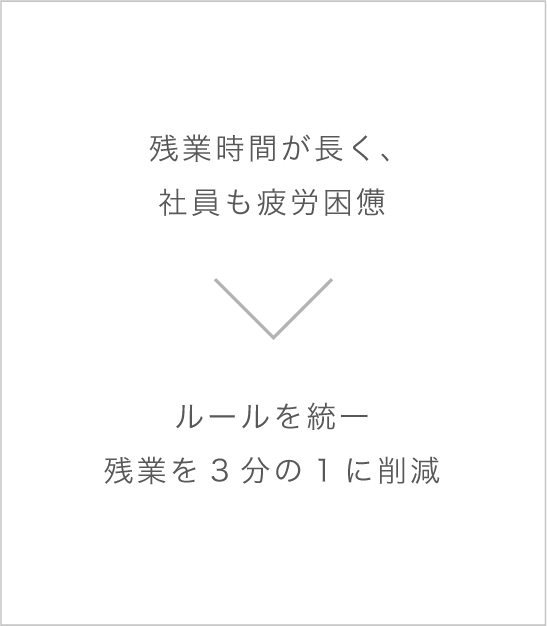
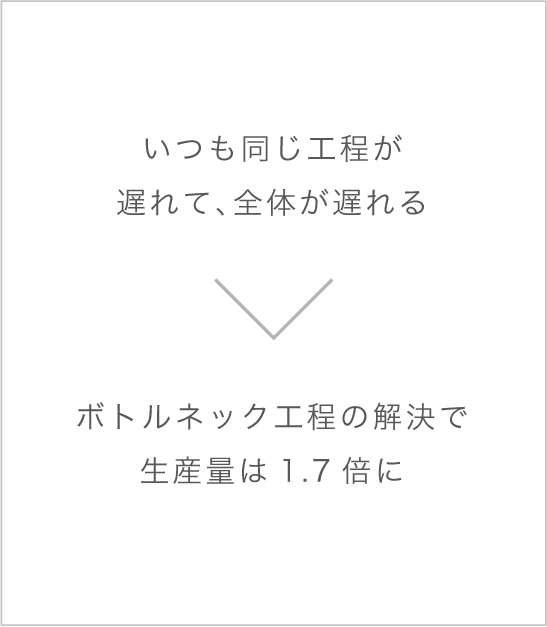
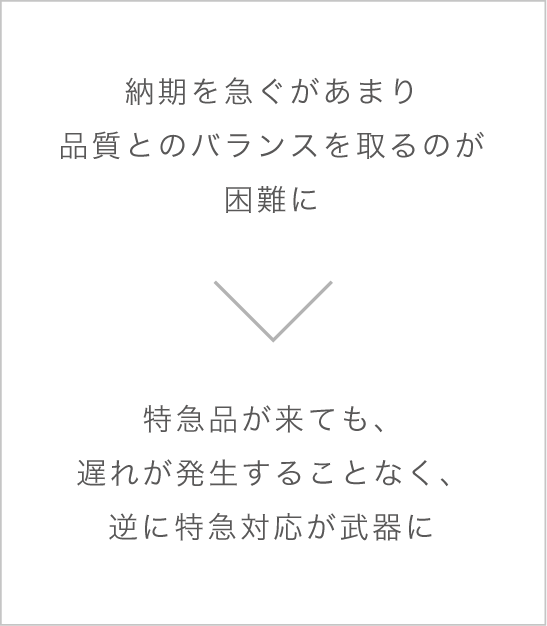
工場を止めて、
徹底的に調査をしてもらいました
Honkiさんに入ってもらう前は、弊社はとにかく残業が多いことが問題でした。
残業をしないと納期に間に合わないので、とにかくみんな残業をして必死に納期に間に合わせる毎日で、みんな疲労困憊になっていました。現場からも「もうこれ以上できない」という声が上がってくるほど。それでも「頑張ろう」としか言えず、非常に苦しい日々でした。
納期を間に合わせることに必死で、そうするとどんどん品質の方が下がってきて、よくないサイクルに陥っていたところ、社長から「Honkiさんに入ってもらう」と言われました。
現場は、社長から言われたらやるしかないのですが、正直戸惑いの声や不安の声が多かったです。今のままではいけないことはわかっていても、今この状況で変化するということは、さらに負担が増えることにもなりかねないので。
まず最初にHonkiさんに入っていただいて行ったことは「工場を止める」ことでした。
これには本当に驚きました。今でも納期を間に合わせることに必死で、残業してまで工場を回している時に、工場を止めたらどうなるか、みんな不安でいっぱいでしたが、結果としては、全く問題がありませんでした。
ただ単に工場を止めたら大変なことになると思いますが、Honkiさんの調査の結果それが最善で、止めてからの動きもHonkiさんの指示のもと動いたので、結果として無駄な動きをなくすことができ、最良の形で再度スタートすることができました。
これには本当に驚きました。自分たちでは絶対にできない判断だと思います。
それでもまだ社員の中では不安や反発の声、戸惑いはありましたが、劇的に残業が減ったことでみんなの意識が徐々に変わっていきました。
それまでは「残業をして当たり前、なんとしても納期を間に合わせる」という意識しか向かなかったのが、効率を考えたり、品質に目を向ける余裕が生まれ、今では品質をしっかり保ちながら納期も守り、さらに残業もない状態で仕事ができています。
Honki TOC導入メリット
工場内を徹底的に調査、
工場を全て見える化し無駄な生産をゼロ に!
ボトルネックを特定し、改善活動へ
物の流れが見える工場は、ボトルネックとなる問題がどこかがすぐわかるようになります。今回は前工程が問題となって、全体の生産に影響を与えていることが発覚しました。そのボトルネックとなる工程の生産力を強化することで、生産量を一気に上げました。
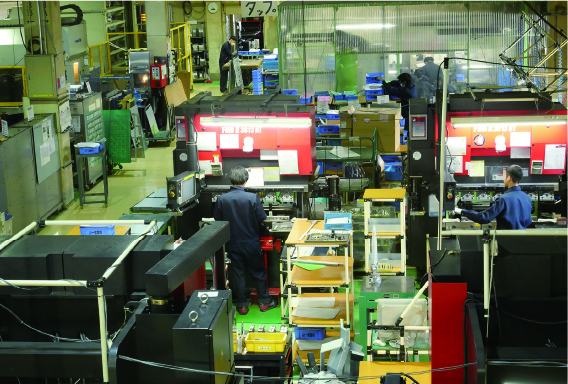
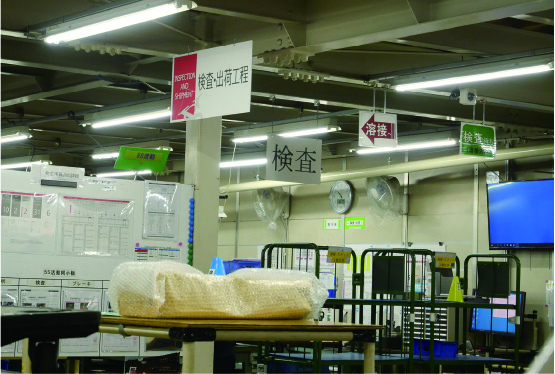
工場調査を実施し、工場の見える化へ
まず工場の調査から入り、仕掛品が溢れかえっている状態を整理することから着手しました。物が溢れかえり「何がどこにあるのかわからない」「探す時間のロス」「急いだのに納期に間に合わない」などの問題が発生していました。仕掛品を置く棚の配置を最適化し、作業員への指導を徹底することで、物の流れが見える工場になりました。
必要な物を必要な時に作り、残業削減へ
必要な物を、必要な時に作り続けることを徹底しました。空いている時間があれば、何か動いていないと不安になる作業員に対しても「無駄な物は作らないように」と指導しました。作業者は、コンサルティングが進むにつれて、残業時間が削減されたことを実感。成果が見えることにより、会社の一体感が高まり、他社に負けない工場へと変化しました。
具体的には、TOCの導入によって残業時間が「52時間/月」だったのが「18時間/月」へ削減、さらに、生産個数は「191個/時」だったものが「329個/時」にアップしました。
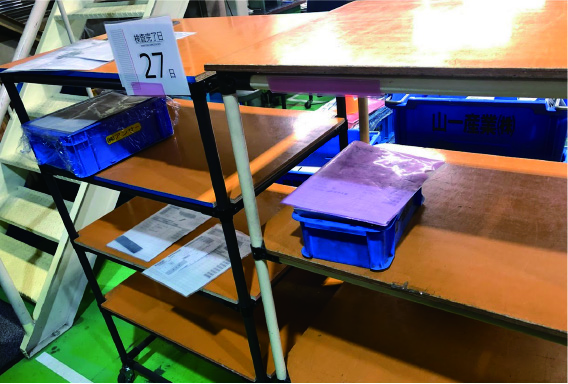
1周目
i
調査
現地調査、ヒアリン グから、曲げ工程が ボトルネックになっ ていることが判明。
P
計画
ボトルネック解消の方法と、解消により得られるメリットを 掲示。
S
勉強
TOC の概念および、ボトルネックである
曲げ工程を改善することの重要性や、ボトルネック工程を改善する方法を学ぶ。
G
実行
計画、勉強した内容に基づき、曲げ工程を改善。
⇒ボトルネック解消
2周目
i
調査
製品作成におけるリードタイムが長いことが判明。
P
計画
リードタイムを大幅に削減する方法を掲示。
S
勉強
リードタイムの大幅な削減による効果と、それによって起きる問題を議論。
G
実行
工場内を工場長に巡回してもらい生産管理を徹底。製品の
リードタイムを大幅に削減。
⇒ボトルネック解消
3周目
●
調査
●
計画